Denim Manufacturing, Part 1: FABRICATION
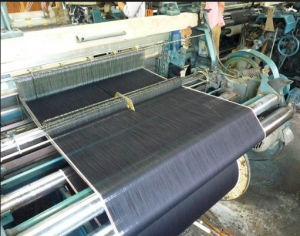
By Anya Ferring
Ah denim! It is with great irony that the fashion industry has managed to take something so seemingly simple (basic cotton work pants that have existed for over a century) and evolve them into one of the most multi-layered garment development and production scenarios out there. While there is much to be said about the alternate universe that is denim, these brief tutorials will focus only on the key elements necessary to take into consideration when developing garments that will eventually be scaled out into production:
- the type of denim fabric that will be used
- the manufacturing processes
- the final garment finishing.
It is vital to have an understanding of all three steps from beginning to end in order to achieve the effect you are looking for with denim product.
DENIM FABRIC:
Dying: Denim, unlike many types of cloth (which are woven in one place and sent to another for dying), is woven and dyed at one location. Yarn that is used for warping is dyed before weaving, often using a synthetic indigo dye—darker shades are achieved by dying the yarn multiple times. Denim is not 100 percent blue, as the blue dyed threads forming the warp (long, vertical threads) are combined with white threads forming the weft (shorter, horizontal threads). Because denim is woven with the blue threads packed closer together than the white threads (see twill weave, below) the blue threads dominate and the cloth registers as blue when viewed on its right side.
The amount of dye used on the threads in the beginning is important because it will affect the level of crocking (which occurs when indigo dye transfers from fabric to another surface due to contact or rubbing), and it will also affect other finishing results which we will discuss further in Part 3.
Weave: Denim is a sturdy cotton warp-faced textile in which the weft passes under two or more warp threads. (If you look at a piece of denim closely you will see the steep diagonal pattern that results from this type of weave, known as a three-by-one right-hand twill weave).
The most common denim is indigo denim, in which the warp thread is dyed, while the weft thread is left white, as we discussed above in the dying section. The size of the yarn used, the fabric weave design, and the fabric tightness will influence the weight of the fabric. This is important because not only will weight affect the drape or feel of the product, but it will also affect the shrinkage rate of the fabric in pre- and post-production.
Fiber: Naturally the fiber content will affect shrinkage as well, so it’s important to note. Though most denim is traditionally 100 percent cotton there are polyester blends available, though cotton will shrink at a higher rate than its synthetic counterparts. Also affecting shrinkage rate is whether the denim has been sanforized, or preshrunk. Preshrunk denim should shrink no more than three percent after three washings.
…So as you can see there is a lot happening at just the fabrication stage. Naturally fiber, dye method, and weave are vital considerations to take when choosing any fabric for any garment, but in denim the effects of shrinkage, weight, and crocking are generally more pronounced than in other fabrics. However if you are aware of all the elements involved, you can use them to your advantage in the design and production process, as we shall see.
Stay tuned next week for Part 2: Manufacturing Denim!